Superprecision sand mould casting industrial method
(IPSC industrial method)
Feature of precise sand mold construction method
Presently, trial manufacture also reaches last stage, the prototype of high accuracy which closer to the die-cast item is required. But, many processes bet on the production, the fact that also cost is rather high is present condition.
Then, our company with the introduction of superprecision sand mould casting industrial method, from start of trial manufacture reached the point where we can actualze the offer the material which is closer to the Die-cast product.
《Feature of IPSC industrial method》
- Precision corresponds to the general tolerance of the metal mold casting.
- In comparison with gypsum casting, cost is the 1/3~3/4.
(However, depend on product shape, there are some differences.)
- The gross production quantity possible up to 400~600, depend on product shape.
- Surface roughness as shown in the paper, is close with the die-cast product.
- Possible to change wooden mould directly, if any design change.
- When starting the trial manufacture, the material which closer to the die-cast product was produced.
- The accuracy is higher than past casting product and the process was less.
Runner |
Equality to Die-cast |
Hot water flow to fillet, corner R |
Surface
accuracy |
Average 25z (Max 15z) |
A necessary part will keep the surface accuracy of 12S and offers the equal product to Die-cast |
Material that
can be used |
AC2A, 2B, 4B, 4C, 7A, 9B, A390, ADC10, AH-14 |
|
Thickness |
Automobile related
Home appliance related |
For Die-cast,
general thickness 2.5mm
Depend on work size,
thickness 2.0mm
Cooling fin,
advanced 1.5mm draft 1 degree |
Production
days |
Mission
(2D:35days, 3D:25days)
Cover
(2D:25days, 3D:15days)
Home appliance
(2D:21days, 3D:15days) |
All machining finishing
Data verification does not include |
Corresponding possible CAD
system |
I-DEAS, UG, CATIA, PRO-E, STEP, IGES, PARASOLID, etc.
possible to correspond to all CAD systems. |
Verification such as draft and thickness before making mould |
Quality
Assurance |
- Size measuring method
- Similar with 3D measurement equipment (contact system)
- Internal defect |
- Cutting, if need
- Leak inspection |
Heat treatment |
In-house T5, T6, T7 |
Corresponds to other heat-treatment if need. |
Impregnation
processing |
Corresponds to the resin and water glass |
|
|
Difference by various casting processes
|
Basic type |
Size accuracy |
Draft |
Cast surface |
Sand casting |
Wooden/Resin type |
1% |
1.5°-3.0° |
50-150z |
Gypsum casting |
Silicon type |
0.3-0.5% |
1.5° |
6-25z |
Precise sand casting
(IPSC) |
Resin type |
0.3-0.5% |
0.5°-1.5° |
15-35z |
|
IPSC method casting surface roughness measurement data
Region with rough cast surface
ROUGHNESS
CUTOFF = 0.8mm
TRAVERSING LENGTH = 2.50mm
MAG. = 2000
Rz = 27.68μm
27.68z
ROUGHNESS
CUTOFF = 0.8mm
TRAVERSING LENGTH = 2.50mm
MAG. = 2000
Rz = 27.68μm
29.99z |
|
General region
ROUGHNESS
CUTOFF = 0.8mm
TRAVERSING LENGTH = 2.00mm
MAG. = 500
Rz = 2.8μm Rmax = 17.9μm Rz = 10.9μm
10.9z
ROUGHNESS
CUTOFF = 0.8mm
TRAVERSING LENGTH = 2.00mm
MAG. = 500
Rz = 3.6μm Rmax = 26.4μm Rz = 14.4μm
14.4.z
ROUGHNESS
CUTOFF = 0.8mm
TRAVERSING LENGTH = 2.00mm
MAG. = 500
Rz = 3.4μm Rmax = 25.7μm Rz = 15.3μm
15.3z |
[The precise sand mould molding] for the problem solving which directed to mass production.
The 3D data is designated faithfulness as shape, trial manufacture process with the [Precise sand mold molding] is a big advance which can verify the problematical point that occurs when mass-producing in Die-cast at trial manufacture step.
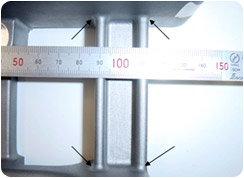 |
 |
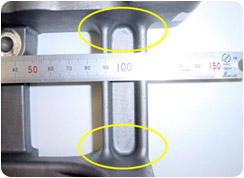 |
A minute crack with the durable test in the precise sand mold prototype due to concentration of stress is generated in the ↑ section. |
|
With the second trial manufacture which is directed to mass production in problem place with the R attaching measure |
[The precision cast product] becomes possible obtaining for reproducibility of thickness and shape the mounting appraisal which equal to the Die-cast.